What is Porosity in Welding: Usual Sources and Effective Remedies
What is Porosity in Welding: Usual Sources and Effective Remedies
Blog Article
Porosity in Welding: Identifying Common Issues and Implementing Finest Practices for Avoidance
Porosity in welding is a pervasive concern that commonly goes unnoticed up until it triggers significant problems with the stability of welds. This usual problem can compromise the toughness and sturdiness of bonded structures, presenting safety threats and bring about expensive rework. By understanding the origin creates of porosity and applying reliable prevention strategies, welders can considerably improve the high quality and dependability of their welds. In this conversation, we will certainly discover the vital elements adding to porosity formation, analyze its destructive results on weld performance, and discuss the best techniques that can be embraced to lessen porosity event in welding procedures.
Common Reasons For Porosity

An additional regular wrongdoer behind porosity is the presence of pollutants on the surface area of the base steel, such as oil, oil, or rust. When these pollutants are not properly removed prior to welding, they can evaporate and come to be entraped in the weld, triggering issues. Additionally, making use of filthy or damp filler materials can present pollutants into the weld, adding to porosity issues. To minimize these common reasons for porosity, comprehensive cleansing of base metals, correct protecting gas option, and adherence to optimal welding parameters are crucial techniques in achieving premium, porosity-free welds.
Effect of Porosity on Weld High Quality

The presence of porosity in welding can significantly compromise the structural integrity and mechanical homes of welded joints. Porosity creates voids within the weld metal, damaging its general strength and load-bearing capacity. These spaces act as stress and anxiety concentration factors, making the weld much more at risk to cracking and failure under used loads. Furthermore, porosity can minimize the weld's resistance to deterioration and other environmental variables, better diminishing its long life and efficiency.
One of the main repercussions of porosity is a decline in the weld's ductility and toughness. Welds with high porosity levels have a tendency to show reduced effect toughness and minimized capability to deform plastically before fracturing. This can be especially worrying in applications where the bonded components undergo dynamic or cyclic loading conditions. Moreover, porosity can impede the weld's capability to properly transfer forces, causing early i loved this weld failure and possible safety and security risks in important frameworks.
Best Practices for Porosity Avoidance
To improve the architectural honesty and quality of welded joints, what details measures can be implemented to decrease the incident of porosity throughout the welding process? Porosity prevention in welding is important to ensure the integrity and strength of the last weld. One reliable technique is proper cleansing of the base steel, getting rid of any contaminants such as rust, oil, paint, or wetness that can lead to gas entrapment. Ensuring that the welding equipment is in good condition, with tidy consumables and appropriate gas circulation prices, can also considerably minimize porosity. Furthermore, maintaining a secure arc and regulating the welding criteria, such as voltage, existing, and take a trip rate, aids develop a regular weld pool that decreases the risk of gas entrapment. Making use of the appropriate welding method for the particular material being bonded, such as changing the welding angle and weapon position, can additionally stop porosity. Regular examination of welds and immediate removal of any type of problems identified throughout the welding process are necessary techniques to avoid porosity and create top notch welds.
Importance of Proper Welding Methods
Executing correct welding techniques is paramount in ensuring the structural honesty and high quality of bonded joints, building on the structure of reliable porosity avoidance procedures. Welding techniques directly influence the overall toughness and longevity of the bonded structure. One crucial facet of appropriate welding strategies is keeping the right warm input. Too much warmth can lead to raised porosity as a result of the entrapment of gases in the weld pool. Conversely, inadequate heat from this source might cause insufficient blend, producing prospective weak points in the joint. Additionally, using the suitable welding parameters, such as voltage, existing, and travel rate, is critical for achieving audio welds with marginal porosity.
Additionally, the option of welding procedure, whether it be MIG, TIG, or stick welding, need to align with the details demands of the job to guarantee optimal outcomes. Correct cleaning and preparation of the base steel, in addition to selecting the best filler material, are additionally crucial elements of efficient special info welding techniques. By sticking to these ideal practices, welders can minimize the danger of porosity formation and generate premium, structurally sound welds.
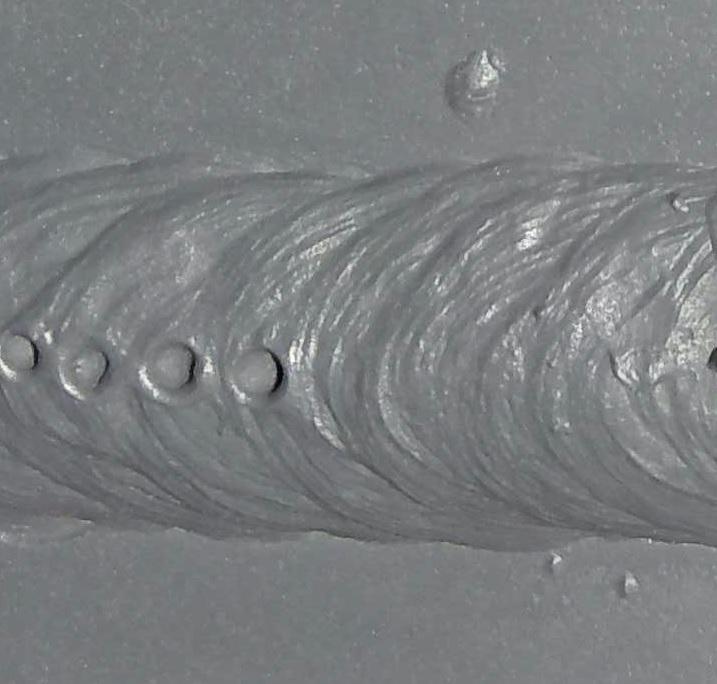
Examining and Top Quality Control Steps
Testing treatments are necessary to spot and prevent porosity in welding, making sure the stamina and durability of the final product. Non-destructive screening approaches such as ultrasonic screening, radiographic testing, and visual evaluation are typically utilized to determine possible flaws like porosity.
Post-weld evaluations, on the various other hand, evaluate the final weld for any kind of defects, including porosity, and validate that it meets specified standards. Carrying out a comprehensive top quality control strategy that includes extensive testing procedures and examinations is extremely important to decreasing porosity issues and making certain the general quality of bonded joints.
Final Thought
To conclude, porosity in welding can be a typical issue that affects the quality of welds. By determining the common reasons of porosity and implementing best techniques for avoidance, such as proper welding techniques and screening measures, welders can make sure top quality and trusted welds. It is vital to focus on prevention approaches to reduce the incident of porosity and preserve the stability of bonded structures.
Report this page